Application Note
High Sensitivity
Gradiometer - Magnetic Anomaly Detection
This note describes the use
of a dedicated IC chip, the SCL007, intended to provide the
essential electronics for the construction of two-sensor
type gradiometers.
While small magnetic field
changes can be readily detected with a single static sensor,
as in the case of an earth field magnetometer, the very
presence of the large earth field presents an immediate
problem if the sensor is to be moved. A small change in
angle will give a signal which is likely to be many times
larger than the field magnitude variations that are being
looked for as anomalies.
The gradiometer principle is
based on the fact that, in a uniform field, two identical
and perfectly aligned sensors will give identical outputs
which can be subtracted from one another to give a zero
output, effectively eliminating the apparent presence of the
field. Provided the sensors remain solidly fixed in relation
to one another, the whole assembly can be rotated in space
without producing any orientational output. If, however,
there is a superimposed small field gradient as well as the
uniform field, the output of the subtracted sensor
combination will change as a function of the magnitude and
direction of that gradient. Such gradients arise from the
presence of anomalous magnetic moments within the capture
range of the gradiometer.
These anomalies may arise
from a great many causes, varying from the tiny firing pin
of a plastic land-mine buried only a few inches under the
surface, to a large marine wreck on the sea bed. The
apparent capture range also varies enormously since it
depends on the magnetic moment of the anomaly. A small pole
strength coupled with a very large object can produce a
large magnetic moment, giving a correspondingly large
capture range. Conversely even a large pole strength in a
very small object can give rise to a very limited capture
range. A typical example of the latter is the modern flat
ceramic type of magnet which is magnetised through is
thickness rather than along its larger dimension. Such
magnets seem very powerful in their grip but produce very
small fields at a distance.
The distance between the two
sensors depends on the distance at which an object of
interest is to be detected, and its magnetic moment. This
spacing should be determined by experiment. For small
targets within 2 feet of the nearest sensor, try a sensor
spacing of 18 inches.
In practice no two sensors
are ever identical and measures must be taken to eliminate
their zero-field offsets and to match their sensitivities.
In practice this is not too difficult to do electronically,
if an initial calibration routine is adopted on switch-on.
This can be semi-automatic and requires only a simple manual
manipulation. It is more difficult however to guarantee the
identical alignment of the sensor axes in the mechanical
sense and for accurate instruments some adjusting mechanism
will be required. This type of adjustment should fortunately
not be necessary at every start-up and should remain
accurate if the gradiometer is constructed from stable
materials.
One method of arranging for
this alignment is to build the gradiometer in a tube of
diameter somewhat larger than that of the sensors. One
sensor is fitted permanently into one end of the tube with
appropriate packing to hold it securely. The other sensor is
fitted to the opposite end of the tube but only held at one
of its ends by some sort of flexible mount such as a snugly
fitting O-ring. Four adjusting (non magnetic ) screws can
the be fitted at right angles around a circumference of the
tube to force the non-clamped end of the sensor to tilt
slightly in the required direction.
The basic idea is illustrated
in the diagram below.
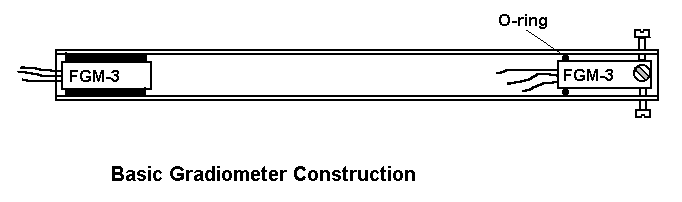
The position of the set
screws can only be determined by experiment, the objective
being to reduce to a minimum the variation of output ( after
electronic calibration ) observed when the gradiometer is
rotated freely in space.
One technique for doing this
is to place the gradiometer tube in V-blocks in an
approximately horizontal east-west direction and gently
rotate the tube about its axis. Since the earth's field
should be at right angles to both sensors in this
configuration any misalignment of the sensors should result
in a sinusoidal variation of output with rotation, giving a
clue as to the required direction of adjustment.
A further source of potential
error is the possibility that the sensors may not have
identical non-linearities. This is less easy to overcome but
an improvement in performance is possible in most cases by
adopting an appropriate usage technique. It will vary with
the application but consists basically of trying always to
hold the gradiometer in the same orientation when making
measurements. For accurate measurements, where speed is not
the prime requirement one good way of doing this is to
suspend the tube vertically from a simple pivot allowing
gravity to guarantee the repeatable alignment. In this way
the gradiometer can be moved over a large grid, for example,
to allow the plotting of contours of gradient in a search
for underground anomalies.
Earth anomalies usually show
up best in the vertical orientation, which is probably why
oil companies and archaeologists make use of the vertical
vector in their studies.
For simpler less accurate
systems used with short ranges, for example metal detectors,
it may be enough to simply maintain a constant orientation
by hand and eye coordination.
The pin layout can be seen in
the schematic diagram below.
Pin 1 is an input giving two
different sensitivities when set either high or low. The two
sensitivities, controlled by pin 1 differ by a factor of
eight to provide a range for larger field anomalies.
Pin 2 is an output pin which
provides a polarity signal as part of the output, which
should therefore be regarded as a signed magnitude, rather
than the usual twos complement. This gives an extra bit of
precision to the reading by effectively making the output a
total of nine bits.
Pins 17 and 18 are the sensor
inputs and accept the 5 volt output pulses directly.
Pins 15 and 16 are for a
crystal circuit to give a stable reference to measure the
sensor period variations against.
The remaining pins are the
digital output bits, D0 to D7 for use by external equipment
or displays. D0 =LSB, D7=MSB
The system performs an auto
calibration during the first ten to twenty (dependent on
crystal frequency) seconds after switch on, during which it
expects to see the maximum and minimum value of the earth's
field. The best way to do this is to hold the gradiometer in
a north-south orientation pointing upwards at about the
angle of the field's inclination, (in the UK about 67°
to the horizontal in the north/south direction) then switch
on and rotate the gradiometer through 180°
to directly reverse its direction, during the ten seconds
after switch on. It is best not to do this any more hastily
than necessary.
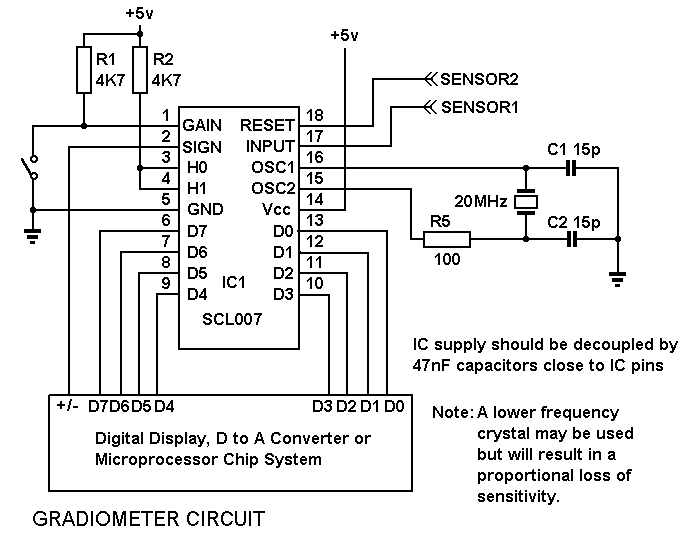
After this the system will
determine the sensitivity and the zero offset for each
sensor separately and correct for the errors, which would
arise through sensor differences, during the signal
subtraction process. It should then be possible to rotate
the gradiometer slowly in any direction without getting too
much output if there are no field anomalies at the location.
It should be done slowly because the sensors are time
multiplexed and rapid movement will beat the system to some
extent.
A little practice at this
technique will soon get the best cancellation and the
process can be repeated as often as necassary to optimise
the balance. Also for the best observations it is obviously
advantageous to always have the sensor in the same
orientation during the taking of readings. You can test the
success of the set-up by approaching the gradiometer with a
permanent magnet as the local anomaly. The size of the
anomaly will be a function of the moment of the magnet which
is a function of its magnetic length.
One other point is worth
mentioning. If you adopt the suggestion of hanging the
gradiometer vertically, then it is an advantage to hang it
from the end that makes the wires from each sensor emerge in
the downward direction.
Two sensors which share the
same 5 volt regulated power supply line impedance can give
rise to a tendency for the individual sensors to frequency
lock together when their output frequencies are within a few
hundred Hertz of one another. This can be eliminated by
decoupling capacitors fitted close to each sensor’s +5V and
Ground pins. Tantalum or electrolytic capacitors of 22 to 47
uF will be adequate. In addition to the capacitors, more
effective decoupling is obtained by running each sensor’s
power and ground leads separately back to the source in
order to minimise a common power supply and ground impedance.
Best results have been
obtained using a rigid non-metallic pipe to mount the two
sensors in. One method to increase the rigidity of plastic
pipe, is to slide a tight fitting piece of aluminum angle
stock into the pipe after first mounting the sensors on it.
Alternatively, the pipe itself may be fastened to a larger
piece of angle stock exterior to the pipe. A close fitting
copper or aluminum pipe may degrade sensor performance by
acting as a "shorted turn" to the sensor’s internal
oscillator. Under no circumstances should an iron or steel
pipe be used as this would severely limit the sensitivity of
the gradiometer.
|